
Quality Objectives
A: Customer Satisfaction Score > 90;
B: Finished Product Acceptance Rate: > 98%.

Quality Policy
Customer First, Quality Assurance, Continuous Improvement.

Quality System
Quality is the foundation of an enterprise, and quality management is a perpetual theme for any successful business. Only by consistently providing high-quality products and services can a company earn long-term trust and support from its customers, thus gaining a sustainable competitive advantage. As a precision components factory, we have obtained ISO 9001:2015 and IATF 16949:2016 quality management system certifications. Under this comprehensive quality assurance system, we are committed to continuously improving product quality and service levels.
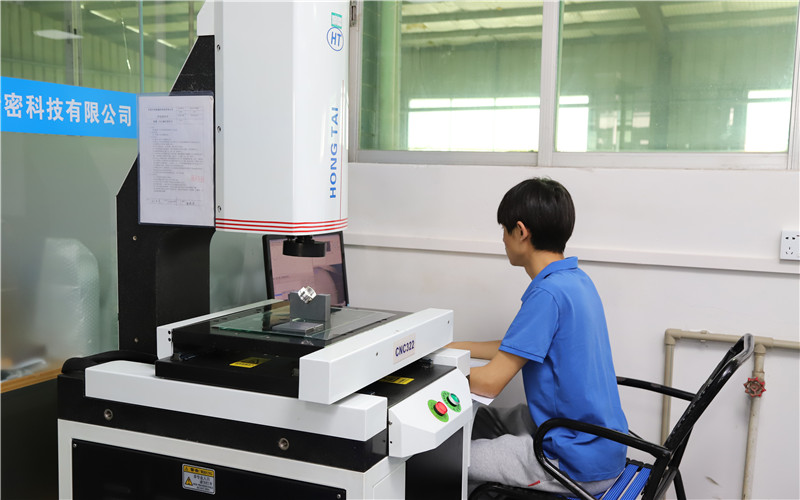
The Quality Department is a vital part of Zhuohang factory. Its responsibilities include establishing quality standards, conducting quality inspections and control, analyzing quality issues, and proposing improvement measures. The mission of the Quality Department is to ensure the qualification and stability of precision components to meet customer needs and expectations.
Zhuohang's Quality Department comprises a dedicated team of professionals, including quality engineers, inspectors, and various other talents. Team members possess extensive industry experience and specialized knowledge, enabling them to effectively address various quality issues and provide customers with professional quality solutions and excellent after-sales service.
The Quality Department is equipped with more than 20 sets of precision inspection devices, including coordinate measuring machines, metal material analyzers, optical measuring instruments, microscopes, hardness testers, height gauges, salt spray test machines, and more. These devices facilitate various precise inspections and analyses, ensuring that product quality complies with relevant standards and customer requirements. Additionally, the Quality Department employs advanced quality management software, such as Statistical Process Control (SPC), to monitor and analyze quality data during the production process.
Through a scientific quality management system and advanced inspection equipment, we guarantee the qualification and stability of product quality.
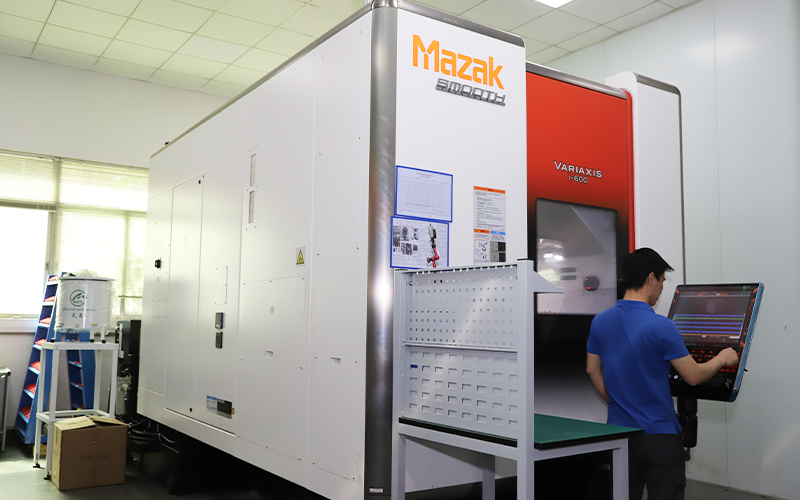
Quality Inspection Steps

Incoming Inspection:
IQC is responsible for inspecting the quality of all raw materials and purchased components to ensure they meet requirements. The inspection process includes verifying the supplier-provided test reports, conducting visual checks, measuring dimensions, performing functional tests, etc. If any non-conforming items are found, IQC promptly notifies the procurement department for return or rework.

In-process Inspection:
IPQC monitors the quality during the production process to ensure products meet quality standards and customer requirements. The inspection process involves patrol inspections, sampling, recording quality data, etc. If any quality issues are detected, IPQC promptly notifies the production department for improvement and adjustments.

Outgoing Inspection:
OQC is responsible for the final inspection to ensure that all finished products meet requirements. The inspection process includes visual checks, dimension measurements, functional tests, etc. If any non-conforming items are identified, OQC promptly notifies the logistics department for return or rework.